Como a RAM é feita?
Já parou para pensar do que a RAM é feita e como a memória é fabricada? Então é agora que você mata a curiosidade. Vamos contar sobre os bastidores do nosso rigoroso processo para fabricar memórias e garantir que você receba produtos da máxima qualidade.
Existem diferentes tipos de memória, mas todas são feitas da mesma forma. Leia aqui sobre as propriedades dos diversos tipos de memória. Para saber mais sobre os diferentes tipos de memória de servidor, leia aqui.
Parte I: Do silício ao wafer acabado
Chips de memória são circuitos integrados com diversos transistores, resistores e capacitores que devem ser formados em cada chip. Esses circuitos integrados, inicialmente, têm a forma de silício, que normalmente é extraído da areia. A transformação de silício em chips de memória é um procedimento meticuloso e minucioso que envolve engenheiros, metalúrgicos, químicos e físicos. A memória é produzida em um local grande chamado de unidade de fabricação de semicondutores (ou "fab", em inglês), que conta com muitos ambientes controlados, como salas limpas. Os chips de memória de semicondutor são fabricados em salas limpas porque os circuitos são tão pequenos que uma poeira minúscula pode danificá-los. A principal unidade da Micron fica em Boise, Idaho, tem mais de 165 mil metros quadrados e conta com salas limpas classes 1 e 10. Em uma sala limpa classe 1, não há mais de uma partícula de poeira a cada pé cúbico de ar, ou cerca de 28 centímetros cúbicos. Para efeito de comparação, um hospital moderno limpo tem cerca de 10.000 partículas de poeira por pé cúbico de ar. O ar dentro de uma sala limpa é filtrado e circulado continuamente. A equipe de produção usa toucas, jalecos e máscaras especiais que ajudam a manter o ar sem partículas.
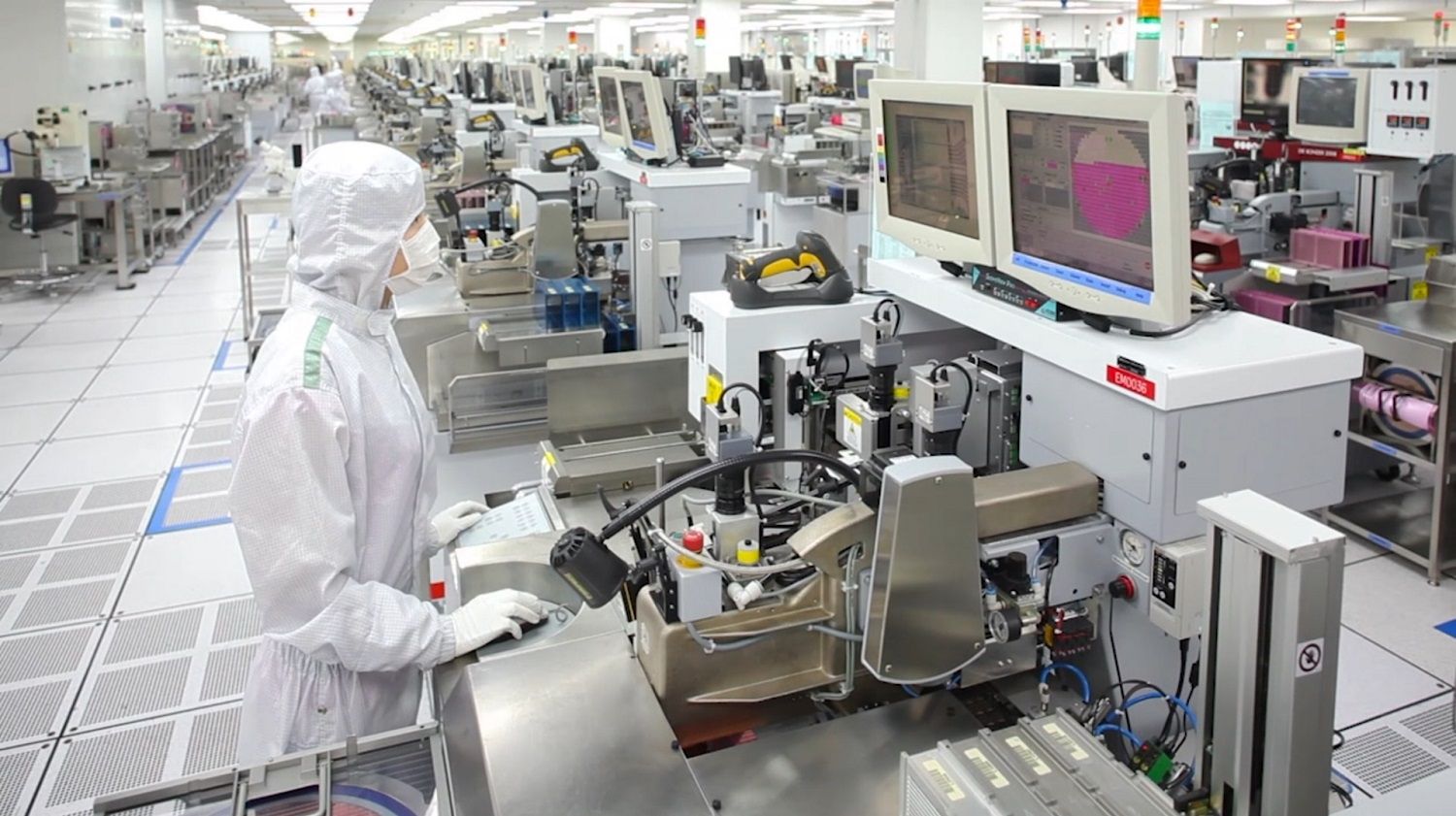
Etapa 1: Lingotes de silício
O primeiro passo do processo de transformação do silício em circuito integrado é a criação de um cilindro monocristalino puro, ou lingote, que é feito de silício e tem 330 milímetros de diâmetro. Depois de formados, os lingotes de silício são cortados em camadas finas e altamente polidas, chamadas de wafers, com menos de seis milímetros de espessura. Em seguida, os elementos do circuito do chip (transistores, resistores e capacitores) são construídos em camadas sobre o wafer de silício. Os circuitos são desenvolvidos, testados em simulação e aperfeiçoados em sistemas de computador antes de serem produzidos. Quando o projeto é concluído, são feitas fotomáscaras de vidro – uma máscara para cada camada do circuito. As fotomáscaras são chapas opacas com furos ou transparências que permitem que a luz penetre em um padrão definido, e elas são essenciais para a próxima etapa do processo de fabricação: a fotolitografia.
Etapa 2: Fotolitografia
No ambiente estéril da sala limpa, os wafers são expostos a um processo de fotolitografia multietapa que é repetido uma vez para cada máscara necessária para o circuito. As máscaras são usadas para (a) definir as diferentes partes do transistor, do capacitor, do resistor ou do conector que completarão o circuito integrado e (b) para definir o padrão de circuito para cada camada sobre a qual o dispositivo é fabricado. No início do processo de produção, wafers de silício puros são cobertos por uma fina camada de vidro, seguida de uma camada de nitreto. A camada de vidro é formada por meio da exposição do wafer de silício ao oxigênio a temperaturas de 900 graus Celsius por uma hora ou mais, dependendo da espessura que a camada precisa ter. O vidro (dióxido de silício) é formado quando o teor de silício do wafer é exposto ao oxigênio. A elevadas temperaturas, essa reação química (chamada de oxidação) ocorre em um ritmo muito acelerado.
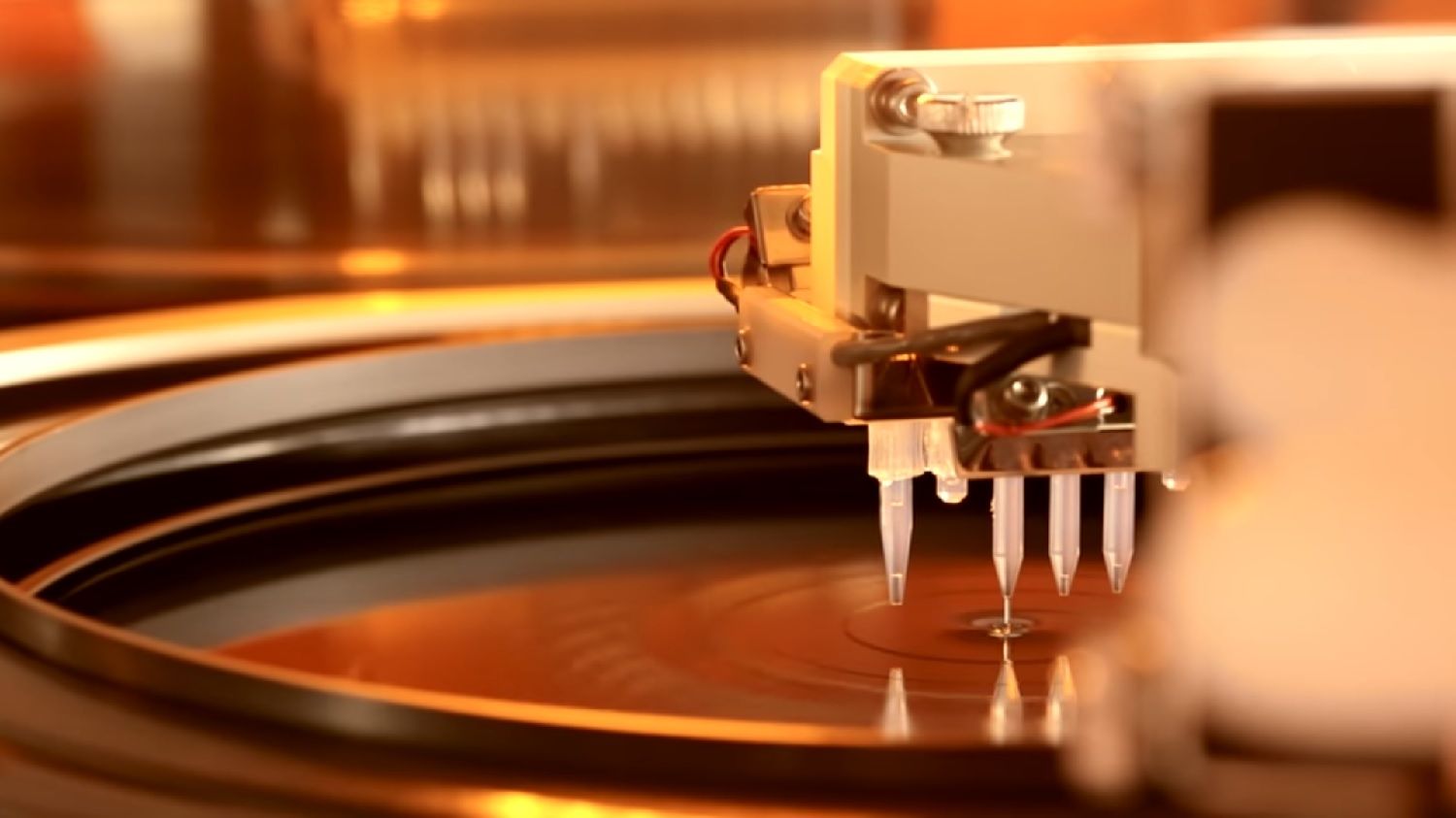
Etapa 3: Fotorresistor
Depois, o wafer é revestido uniformemente com um líquido espesso e sensível à luz chamado fotorresistor. Partes do wafer são selecionadas para a exposição alinhando cuidadosamente uma máscara entre uma fonte de luz ultravioleta e o wafer. Nas áreas transparentes da máscara, a luz penetra e expõe o fotorresistor. Quando exposto a luz ultravioleta, o fotorresistor passa por uma modificação química, que permite que uma solução do desenvolvedor remova o fotorresistor exposto e deixe a parte não exposta no wafer. Os processos de fotolitografia e do fotorresistor são repetidos para cada máscara necessária para o circuito.
Etapa 4: Gravação
Na etapa de gravação, aplica-se ácido a úmido ou gás de plasma seco ao wafer para remover a parte da camada de nitreto que foi desprotegida pelo fotorresistor endurecido. Isso cria um padrão de nitreto no wafer com desenho exatamente igual ao da máscara. Quando o fotorresistor endurecido é removido (limpo) com outra substância química, centenas de chips de memória passam a poder ser gravados no wafer.
Parte II: Aplicação de camadas ao wafer e conclusão do circuito
Na Parte I do processo de produção, todos os elementos do circuito (transistores, resistores e capacitores) foram construídos durante as operações iniciais de máscara. Os próximos passos conectam esses elementos com a criação de um conjunto de camadas.
Etapa 5: Aplicação de camadas de alumínio
Para começar a conectar os elementos do circuito, uma camada isolante de vidro (chamada de BPSG, ou vidro borofosfosilicato) é aplicada sobre o wafer, e uma máscara de contato é usada para definir os pontos de contato (ou janelas) de cada um dos elementos do circuito. Após a gravação das janelas de contato, todo o wafer é coberto por uma fina camada de alumínio em uma câmara de jateamento. Quando uma máscara de metal é aplicada à camada de alumínio, uma rede de finas conexões ou fios de metal é formada, dando origem a um caminho para o circuito.
Etapa 6: Aplicação de camadas de passivação
Em seguida, todo o wafer é coberto com uma camada isolante de vidro e de nitreto de silício para proteger contra contaminação durante a montagem. O revestimento de proteção é chamado de camada de passivação. Uma máscara final e um processo de gravação de passivação acontece, removendo o material de passivação dos terminais, que são chamados de blocos de ligação. Depois de livres, os blocos de ligação são usados para conectar eletricamente o chip aos pinos de metal sobre o revestimento de plástico ou cerâmica e, com isso, o circuito integrado é considerado completo. Antes de o wafer ser enviado para montagem de chips, todos os circuitos integrados do wafer são testados. Nesta etapa, chips em bom funcionamento e com defeito são identificados e mapeados em um arquivo de dados de computador. Em seguida, uma serra de diamante corta o wafer em chips separados. Os chips com defeito são descartados e o resto está pronto para a montagem. Esses chips isolados continuam sendo chamados de chips. Antes do encapsulamento dos chips, eles são instalados em estruturas de chumbo que têm fios finos de ouro conectando os blocos de ligação do chip à estrutura para criar um caminho elétrico entre o chip e as lâminas de chumbo.
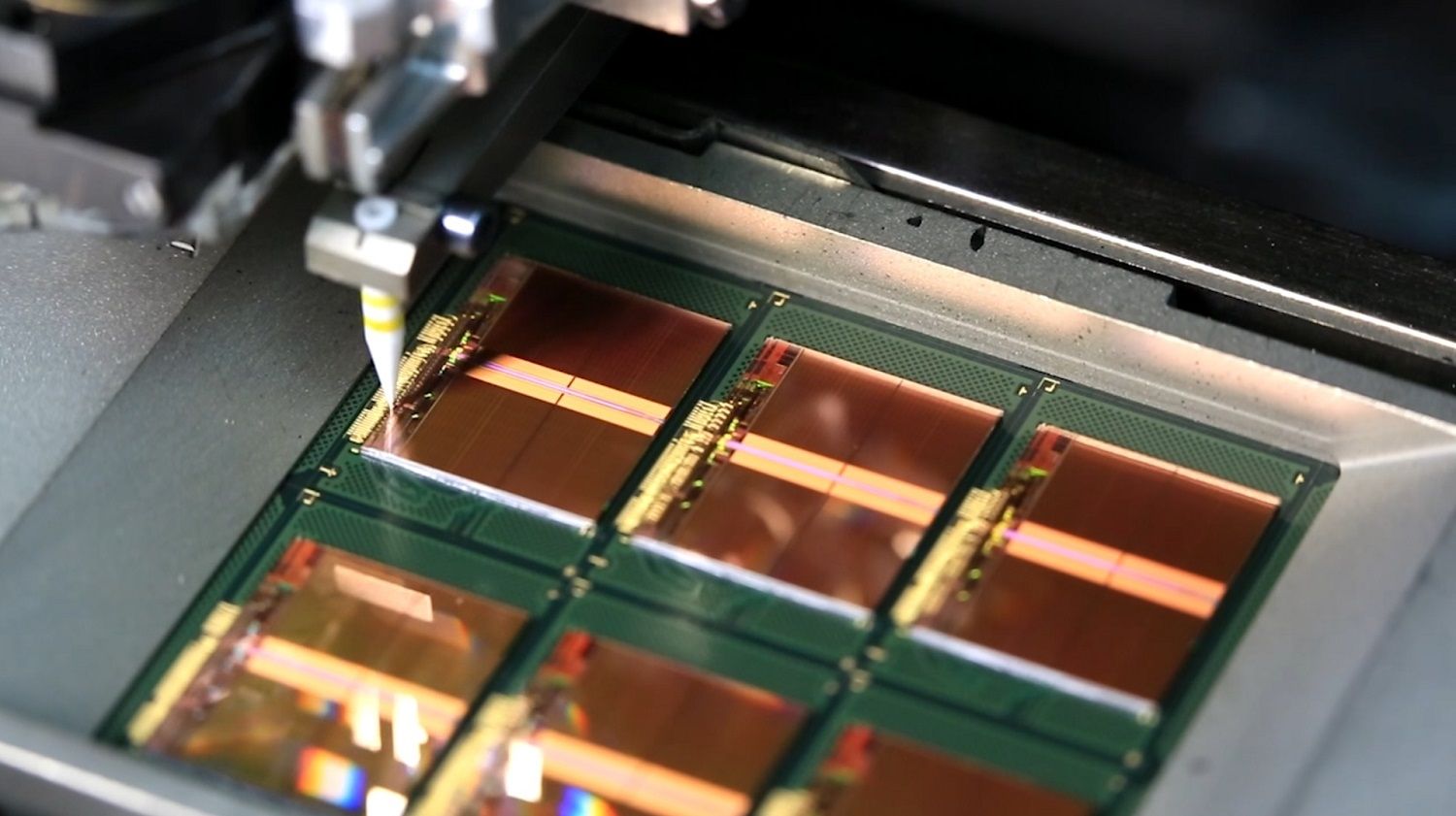
Parte III: Preparação e teste do chip
Na Parte II do processo de fabricação, o circuito integrado foi criado e o wafer acabado foi cortado em chips isolados. Os próximos passos preparam o chip para uso em módulos acabados.
Etapa 7: Encapsulamento
No encapsulamento, as estruturas de chumbo são colocadas em placas de molde e aquecidas. O material plástico derretido é pressionado nas bordas de cada chip para formar seu revestimento. O molde é aberto e as estruturas de chumbo são retiradas e limpas.
Etapa 8: Galvanização
A galvanização é o processo seguinte, em que as estruturas de chumbo encapsuladas são "carregadas" enquanto submersas em uma solução de estanho e chumbo. Aqui, os íons de estanho e chumbo são atraídos para a estrutura de chumbo eletricamente carregada, o que cria um acúmulo uniforme banhado, aumentando a condutividade do chip e criando uma superfície limpa para que o chip possa ser montado.
Etapa 9: Acabamento e formato
No acabamento e formato, as estruturas de chumbo são inseridas em máquinas de acabamento e formato, onde são formados os contatos e os chips são separados das estruturas. Em seguida, os chips isolados são colocados em tubos antiestáticos para manuseio e transporte até a área de teste para a realização dos testes finais.
Etapa 10: Teste de estresse
No teste de estresse, os chips são testados quanto a seu desempenho em condições de uso intensivo acelerado. O teste de estresse é um componente essencial da solidez do módulo. Por testar módulos em condições de uso intensivo acelerado, podemos eliminar os poucos módulos de cada lote que falham após uso mínimo. Para realizar o teste de estresse, usamos fornos AMBYX de ponta que nossos engenheiros desenvolveram especificamente para esse fim. Após aprovados no teste de estresse, os chips de memória são inspecionados, vedados e preparados para a montagem.
Etapa 11: Montagem e construção da PCB
Com os chips de memória produzidos, é necessário dar a eles uma forma de se conectar à placa-mãe do computador. As placas de circuito impresso (PCB) resolvem esse problema oferecendo uma forma para conectar os chips à placa-mãe. Para fazer isso, os chips são instalados em uma placa de circuito impresso (PCB), e o produto final é um módulo de memória acabado. As PCBs são matrizes integradas, ou lâminas, compostas de diversas placas idênticas. Após a montagem, a matriz é separada em módulos, exatamente como uma barra de chocolate pode ser dividida em quadrados menores. Ao variar o total de PCBs em cada matriz de acordo com o tamanho, a Micron maximiza o número de módulos produzidos com uma determinada quantidade de matérias-primas.
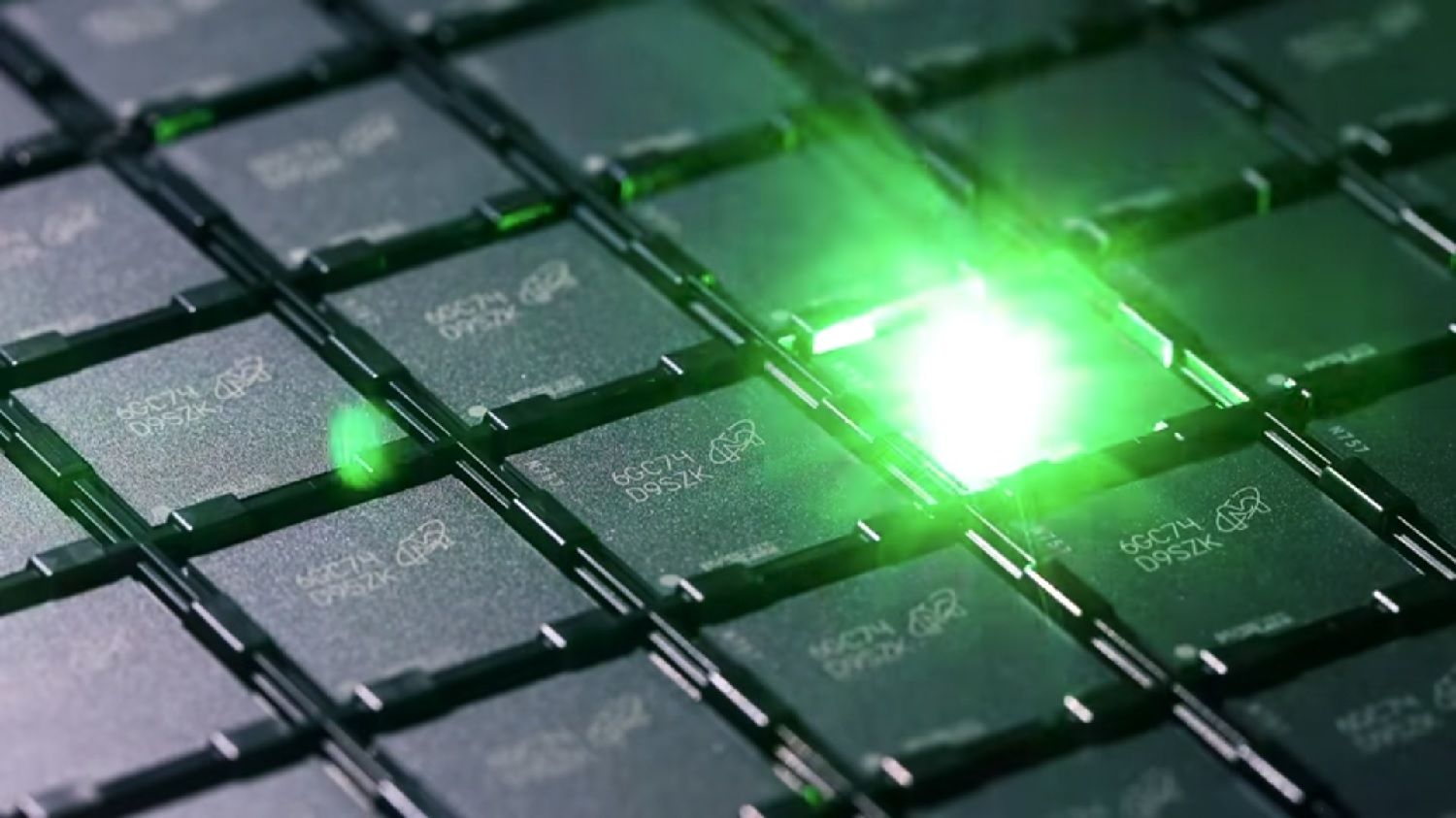
Parte IV: Montagem do módulo
Na Parte III do processo de fabricação, o chip e a PCB foram preparados para a montagem do módulo final. Os últimos passos envolvem o processo de montagem do módulo.
Etapa 12: Serigrafia
Quando o desenho do módulo é aperfeiçoado e as PCBs são produzidas, começa a montagem do módulo de memória! A montagem envolve um complexo procedimento de soldagem que fixa os chips de memória à PCB. Esse processo começa com a serigrafia. Na serigrafia, um estêncil é usado para aplicar pasta de solda à PCB acabada. A pasta de solda é uma substância viscosa que fixa o chip à PCB. O uso do estêncil garante que a pasta de solda seja fixada somente nos locais em que os componentes (chips) serão encaixados. Os pontos de encaixe são fáceis de encontrar graças aos fiduciais, que são marcas na PCB que determinam o local em que os chips devem ser colocados. Após a aplicação da pasta de solda, as máquinas de colocação automatizadas identificam os fiduciais para determinar em que pontos da PCB devem colocar os chips. As máquinas de colocação são programadas para saber o local específico de cada chip, assim, quando uma máquina coleta um chip da esteira e posiciona sobre a PCB, ela sabe exatamente onde o chip está. O processo de colocação de chips ocorre para todos os chips restantes e todos os demais componentes do módulo. De todas as etapas da produção de memória, esta é a mais rápida: os chips são colocados na PCB acabada em questão de segundos.
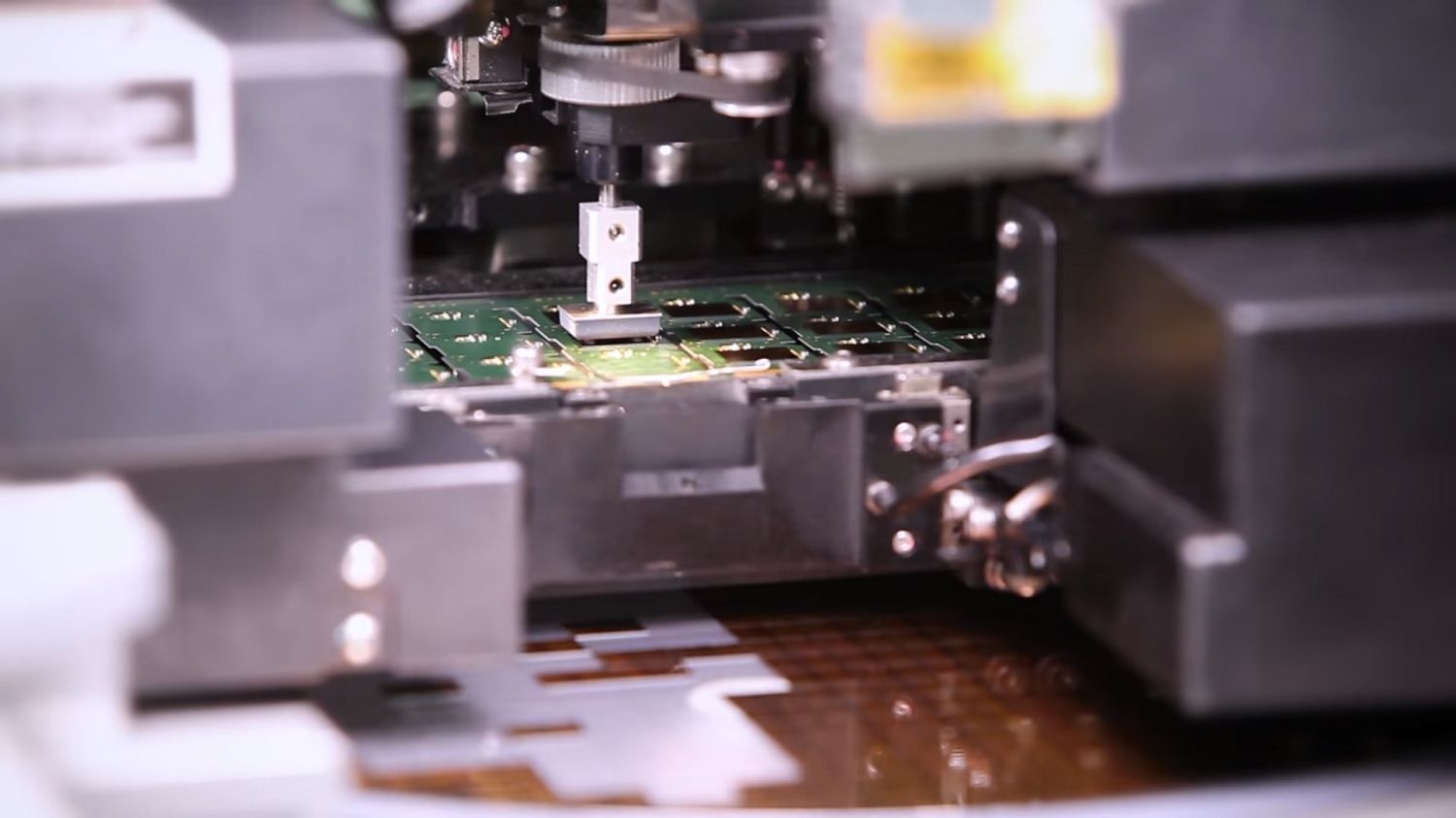
Etapa 13: Soldagem e fixação
Em seguida, os chips montados e as placas passam por um forno. O calor derrete a pasta de solda, transformando-a em líquido. Com o resfriamento da solda, ela se solidifica e cria uma cola permanente entre os chips de memória e a PCB. A tensão da superfície da solda derretida impede que os chips se desalinhem durante o processo. Depois da fixação dos chips, a matriz é separada em módulos. A equipe da Micron inspeciona cada módulo visualmente. Muitos módulos ainda são submetidos à inspeção adicional usando equipamento de raio-X automatizado para garantir que todas as junções foram soldadas corretamente. Todos os módulos de memória da Micron atendem aos critérios de aceitação IPC-A-610, o padrão do setor reconhecido internacionalmente.
Etapa 14: Teste de qualidade pós-montagem
Em seguida, a Micron testa e aplica a identificação aos módulos. Usamos equipamentos exclusivos para testar o desempenho e o funcionamento deles automaticamente. Assim, eliminamos qualquer possibilidade de um operador, por acidente, colocar um módulo com defeito na área de aprovados. Alguns módulos são programados com uma "placa de identificação" que seu computador possa reconhecer e ler.
Etapa 15: Expedição
Antes de ser enviada a fabricantes de computador e consumidores, uma parcela estatisticamente significativa dos módulos acabados é selecionada aleatoriamente para uma inspeção de qualidade final. Depois da aprovação para uso, os módulos são colocados em compartimentos e sacos plásticos à prova de descarga eletrostática e estão prontos para a expedição. Após um exaustivo processo de fabricação, sua memória está pronta para usar. E ela foi rigorosamente testada e aprovada! Para saber mais sobre unidades de memória, leia aqui!
©2018 Micron Technology, Inc. Todos os direitos reservados. As informações, os produtos e/ou as especificações estão sujeitos a alterações sem aviso prévio. A Crucial e a Micron Technology, Inc. não se responsabilizam por omissões ou erros tipográficos ou fotográficos. Micron, o logotipo da Micron, Crucial e o logotipo da Crucial são marcas comerciais ou registradas da Micron Technology, Inc. Todas as demais marcas comerciais e marcas de serviço pertencem a seus respectivos proprietários.